The history of modern industry today normally associated with modern day production philosophies like Just In Time and Lean Production were under development or available in the mid 19th century (Cammarano, 1997). Manufacturing System is one of the challenging and complex operation composed of large area of interactions between people, materials, machines, information and environment in the process of wide variety of products. It represents the way an individual use technology at work in planning, designing, implementing, and controlling the systems. Manufacturing system design is broad and are characterised by an obligation to combine into a whole both the physical and decision making competent of humans together with all other feature of the system design. Most of the manufacturing systems are complex, so that major design or redesign is a demanding task for today’s market. The engineers and managers who are faced with this task can find guidance in recognised principles of good manufacturing system design (Suresh and Kay 1998), they can learn from observations of successful organisations (Womack et al. 1990), and they can tailor this knowledge to their own organisations using structured analysis and design methods (Mills et al. 1996). These design methods all have some form of evaluation, usually based on a combination of analysis, judgement and bargaining be
tween the practitioners involved (Mintzberg et al. 1976).
Model never completely reflect reality, reality is always more abundant. The only models that will inspire some confidence, sometimes, are large, detailed optimisation and simulation models (Meal, 1984). An analytical tool that is a valuable aid to manufacturing system design is simulation modelling. Simulation is mostly used to undertake a comparative analysis of system designs. Now, Simulation is an important part of a design or redesign process, especially in the manufacturing system. Since researchers specialise in determining individual capabilities and limitations, they can identify changes that may improve overall system performance and implement and test these proposed changes in a simulator (Arbak, Derenski and Walrath, 1993). Simulation is a coarse replication of the dynamic behaviour of the proposed system; it produces numerical performance indicators, and enables the practitioner to make informed judgements about the proposed system (Baines, Ladbrook, 2002). In other word, modelling is also known as applying a technique such as Discrete Event Simulation (DES) (Carrie 1988, Robinson, 1994). In manufacturing system design, computer based animation is widely used to build.
DES is most frequently used to use the elements of a manufacturing system that are highly deterministic in their behaviour, usually mechanical equipment such as machines, conveyors and robotics. DES model define an individual/people as a resource which is needed by activities such as machining and assembly to take place. In Some cases, modelling aids regard human issues as ergonomics. Health and Safety Executive have also issued some general guidelines on work place of manufacturing system. There is other modelling techniques also exist in manufacturing system analysis. Baines et al. (1998) examines schematic representations (e.g. IDEF0), mathematical modelling (e.g. Queuing Theory), and other simulation techniques such as System Dynamics (SD). Among those modelling, SD is a powerful, if occasionally overlooked, technique for manufacturing system modelling (Baines and Harrison 1999). Baines and Ladbrook (2002) also recognise that there is an important need to expand the capability of modelling to include the relationships between people, their working environment, and their subsequent performance in terms of productive routines. This will be a valuable aid to engineers and managers involved with manufacturing system design or redesign.
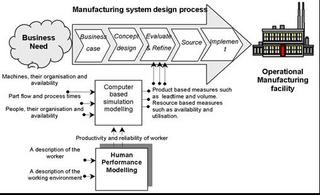
Model never completely reflect reality, reality is always more abundant. The only models that will inspire some confidence, sometimes, are large, detailed optimisation and simulation models (Meal, 1984). An analytical tool that is a valuable aid to manufacturing system design is simulation modelling. Simulation is mostly used to undertake a comparative analysis of system designs. Now, Simulation is an important part of a design or redesign process, especially in the manufacturing system. Since researchers specialise in determining individual capabilities and limitations, they can identify changes that may improve overall system performance and implement and test these proposed changes in a simulator (Arbak, Derenski and Walrath, 1993). Simulation is a coarse replication of the dynamic behaviour of the proposed system; it produces numerical performance indicators, and enables the practitioner to make informed judgements about the proposed system (Baines, Ladbrook, 2002). In other word, modelling is also known as applying a technique such as Discrete Event Simulation (DES) (Carrie 1988, Robinson, 1994). In manufacturing system design, computer based animation is widely used to build.
DES is most frequently used to use the elements of a manufacturing system that are highly deterministic in their behaviour, usually mechanical equipment such as machines, conveyors and robotics. DES model define an individual/people as a resource which is needed by activities such as machining and assembly to take place. In Some cases, modelling aids regard human issues as ergonomics. Health and Safety Executive have also issued some general guidelines on work place of manufacturing system. There is other modelling techniques also exist in manufacturing system analysis. Baines et al. (1998) examines schematic representations (e.g. IDEF0), mathematical modelling (e.g. Queuing Theory), and other simulation techniques such as System Dynamics (SD). Among those modelling, SD is a powerful, if occasionally overlooked, technique for manufacturing system modelling (Baines and Harrison 1999). Baines and Ladbrook (2002) also recognise that there is an important need to expand the capability of modelling to include the relationships between people, their working environment, and their subsequent performance in terms of productive routines. This will be a valuable aid to engineers and managers involved with manufacturing system design or redesign.
No comments:
Post a Comment